Pentru majoritatea producatorilor auto, o schimbare importanta la nivelul companiei o reprezinta o reproiectare a designului masinilor sau orientarea catre pietele emergente. BMW duce lucrurile insa chiar mai departe si mizeaza o buna parte din viitorul brandului pe fire din fibra de carbon, potrivit Bloomberg BusinessWeek.
Firele din fibra de carbon sunt mai subtiri decat parul omului si mai rezistente decat otelul, asa ca BMW le-a folosit deja in modelul sau electric i3, care a intrat pe piata nemteasca in urma cu o saptamana.
Carbonul era folosit in productia avioanelor foarte puternice si a bolizilor de Formula 1, dar poate deveni acum un trend pentru masinile de pretutindeni, cea mai mare schimbare de la introducerea primelor sasiuri facute in totalitate din aluminiu, in anii ’80.
Productia are loc in fabrica de 100 de milioane de dolari dintr-o zona rurala a Washingtonului, unde firele de carbon sunt intinse, ranforsate si apoi prelucrate pentru a se transforma in fibra de carbon.
“Decizia BMW de a lua taurul de coarne si de a crea masini electrice care sa aiba caroserii din carbon este una curajoasa. Ne reaminteste ca gandesc mai mult pe termen lung decat competitia”, spune Sanford C. Bernstein, analist la Max Warburton.
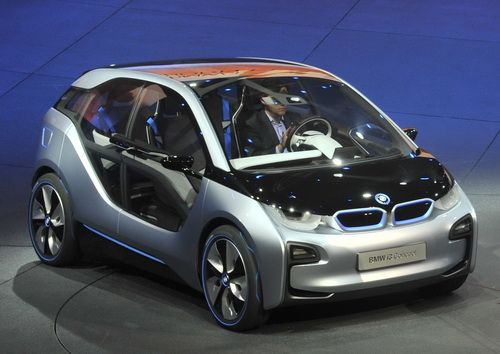
Conceptul BMW i3, realizat partial din fibra de carbon
Strategia a inceput sa prinda contur in urma cu sase ani, cand directorii producatorului auto de lux au ajuns la concluzia ca este cazul sa faca ceva in legatura cu problemele de mediu. De fapt, acestia s-au temut ca noile reglementari din industrie ar putea sa le afecteze afacerea.
“Uitandu-ne catre anul 2020, am observat unele amenintari pentru modelul nostru de business. A trebuit deci sa gasim o modalitate prin care sa aducem modelele seriei 6, seriei 7 si X5 in viitor”, explica oficialii BMW.
Problema cu masinile electrice era faptul ca era nevoie de o baterie foarte mare si grea, ca sa fie capabila sa propulseze autovehiculul. Ca sa contrabalanseze acest lucru, era imperios necesar sa se modifice dimensiunile caroseriei. Cel mai usor si mai puternic material care ar fi putut face asta era fibra de carbon.
Dezavantajul folosirii acestui material este insa costul, cam de 20 de ori mai mare decat in cazul otelului, potrivit firmei de consultanta Frost & Sullivan. Asa ca producatorul auto a decis sa si-l construiasca singur, o decizie mai rar intalnita in industria auto moderna de azi, care se bazeaza pe distribuitori din afara.
“Abordarea BMW ne aduce aminte de perioada revolutiei industriale, cand producatorii incepeau cu prelucrarea fierului in stare bruta sau isi amplasau fabricile in apropierea surselor de putere. Este o abordare agresiva si ramane sa vedem daca va da rezultate”, spune Aravind Chander, analist la Frost & Sullivan.
Sursa: InCont.ro